Commissioning a Process Plant, doing it right to ensure Process Safety
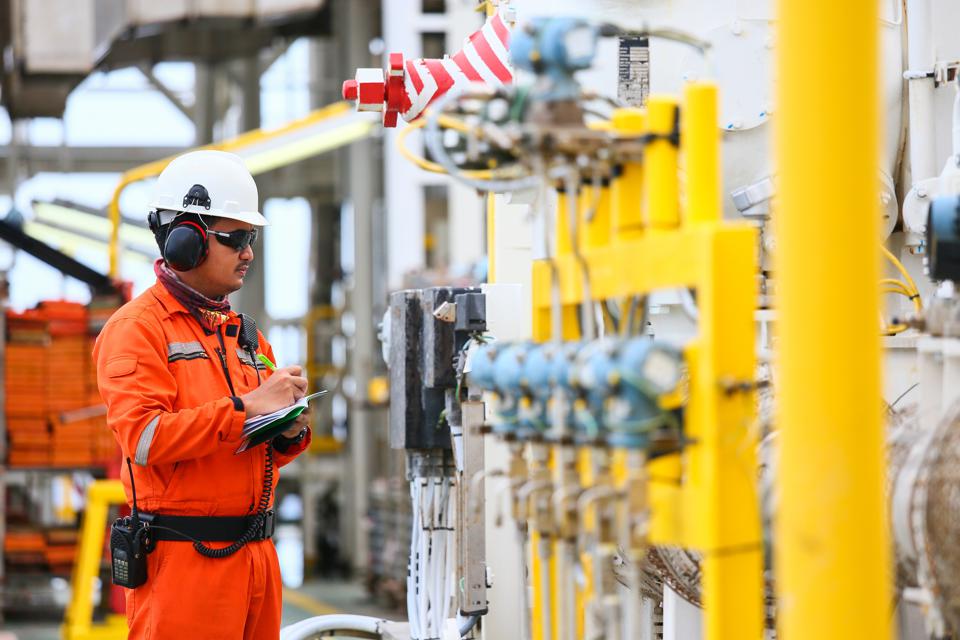
The commissioning of a process plant involves undertaking tests on the plant prior to it going into production in order to determine that it will function adequately and safely.
The commissioning process also includes training the people who will operate the plant as well as the control room staff who will oversee operations. Finally, it includes writing the operating procedure document.
During this commissioning period, when operating experience is at a minimum, the possibility of unforeseen events occurring cannot be eliminated. Consequently, all safety precautions should be reviewed prior to commissioning commencing. This is normally undertaken at the design stage of the plant and usually takes the form of a Hazard and Operability (HAZOP) study or an equally extensive and in-depth risk assessment.
The process of commissioning involves taking the plant through a number of phases, all of which have to be completed in a satisfactory manner before the plant can be handed over as fully functional and ready for operational use.
A typical sequence of phases undertaken during the commissioning process is set out below.
- The system configuration is checked – Walking the Line.
- The pipework and system integrity is checked.
- The instrumentation system is checked.
- All alarms are verified as working.
- All lines and vessels are flushed and cleaned.
- All ancillary equipment is inspected and assessed as to its adequacy.
- All instruments and vessels are calibrated.
- The start- up protocol is established.
1. Walking the Line
This phase is where all the pipework and connections are physically inspected to ensure their configuration is as it should be and that they have been installed correctly.
This inspection is made against Engineering Line Diagrams (ELDs) also known as ‘as built’ drawings. The inspection process also includes ensuring the plant and equipment are clean, empty, and fit for purpose.
2. Checking Pipework and System Integrity
This phase is where all the parts of the system are pressure tested to ensure there are no leaks or unexpected deformities. This is usually undertaken using hydrostatic testing techniques.
Hydrostatic testing is a system that tests the integrity of plants and equipment, including pipework, which will be subject to pressure under normal working conditions.
It involves filling individual sections or components of the system with a liquid, usually dyed water, and then pressurizing that section or component. Pressure is then monitored to see if there is any unexpected deformity or loss of pressure. A loss of pressure would indicate a leak, and the fact that the water is dyed will help locate any leak.
Once all the sections and components have been individually tested, all the sections and components are connected and a test of all the flanged joints and couplings is carried out. This is carried out using nitrogen and trace gas in order to detect any leaks.
3. Checking Instrumentation System
This phase is where the system is checked against the Piping and Instrumentation Diagrams (P&IDs). A P&ID is a schematic drawing showing the physical sequence of equipment and systems, as well as how these systems connect. Included in the P&IDs are:
- All the instruments, their location, and designation
- All the mechanical equipment with their names, numbers, and functions
- All the valves with their identification and function
- All the piping with their sizes and identification
- Any miscellaneous equipment such as vents, drains, sampling lines, etc.
- Start-up and flush lines
- The direction of flow
- Any interconnection references
- All control inputs, outputs, and interlocks
- All computer control system inputs
- Any identification references of components and sub-systems delivered by third parties
4. Verification of Alarms
This phase is where all the alarm settings, microprocessor signals, hardware trips, and all other instrumentation are checked to ensure they are set correctly and functioning as required. The computer systems are also checked to ensure they are functioning properly and that information from all the field instruments is being relayed to the computer interfaces and is being displayed correctly.
5. Flushing and Cleaning of Lines and Vessels
This phase is where all the vessels and associated pipework are flushed through with water in order to flush away any contaminant material. The process is also aimed at ensuring there are no foreign items or materials within the system which may have been left behind at the time of construction.
Once the flushing operation has been completed, it may be necessary to dry the system completely, especially if the final process system is incompatible with water. This is done by venting warm, dry air through the system so that any residual moisture is evaporated away.
6. Inspection and Assessment of Ancillary Equipment
This phase is where all the ancillary equipment, such as pumps, fans, heat exchangers, condensers, compressors, etc. are tested to ensure they perform to their expected requirements.
7. Calibration of Vessels and Instruments
This phase is where all the vessels and instruments are checked to ensure they have been calibrated correctly.
8. Establishing Start- up Protocol
This phase is where the procedure for starting up the installation from complete shutdown to full production is evolved and set down in writing. This phase also includes establishing all potential erroneous occurrences and providing guidance on the best and safest course of action on how to deal with each of them.
This start-up procedure will form part of the ‘operating procedure’ document.
This phase will also involve the training of all personnel involved in the operation of the system once it is handed over.
9. Establishing Shutdown Protocol
This phase is where the procedure for shutting down the installation from being in full production to complete shutdown is evolved and set down in writing.
This phase also includes establishing all potential erroneous occurrences and providing guidance on the best and safest course of action on how to deal with each of them. This shutdown procedure will form part of the ‘operating procedure’ document.
This phase will also involve the training of all personnel involved in the operation of the system once it is handed over.
10. Commissioning Trials
This phase is where the plant is started up, run for a predetermined length of time within specific parameters, and then shut down. This is so the plant can be proven to be operational. It is also an ideal opportunity to give some ‘hands-on’ training to the personnel who will be operating the plant once it is handed over.
11. Hook-up
This is the phase where the system is connected to – although isolated from, until the initial start-up procedure is ready to be undertaken, its source of the product (oil, gas, etc.). It also includes the system being connected to – but again being isolated from – the utilities needed to operate the system.
12. Handover
This is the final phase of the commissioning process and involves handing over the responsibility for the plant, as well as the plant itself, to the operational department.
All associated documents, drawings, and procedures will also be handed over.
During the premier run of the plant, it is quite normal for representatives of the suppliers of the plant and/or equipment to be present or on hand.