Safety Critical Equipment
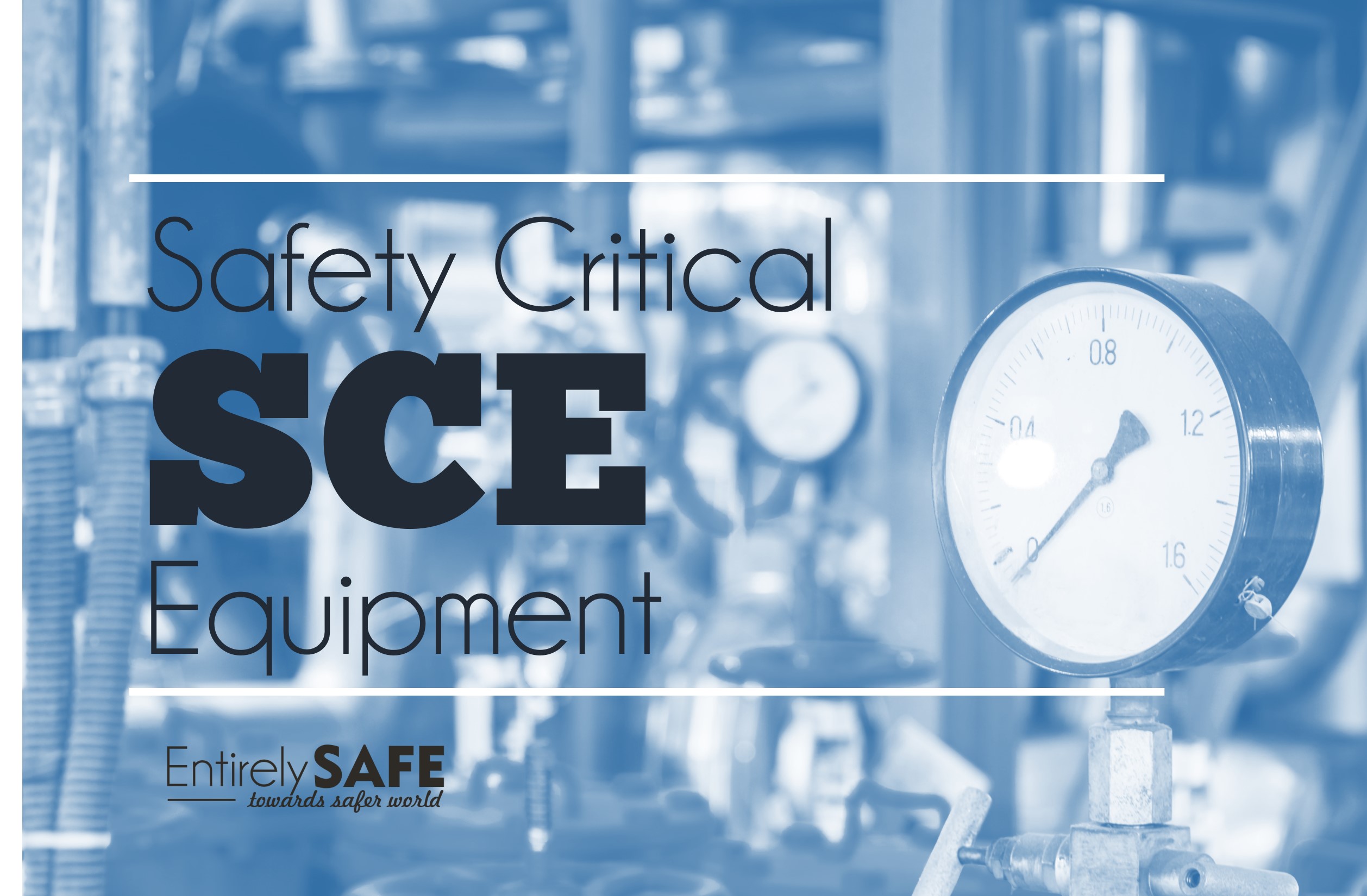
Why we need to Identify Safety Critical Equipment
To ensure that all hardware barriers, which are necessary to control & mitigate Major Accident Hazards, are correctly identified in the Asset Register at the appropriate level of granularity, and classified into the most relevant SCE group.
If is imperial to describe the level at which the performance standards must be established and managed at.
All maintainable equipment needs to be identified for the SCE and non SCE category and registered in Premeventive Maintenance System to develop the maintenance program.
Sequence of actions to get your SCE failure Prevention system up and running
Provide structural and load bearing support to handle drilling operations within the equipments safe operating envelop and inspection of that equipment to prevent failure that may result in structural damage, personal injury or loss of containment
Boundary Conditions Drilling Systems
The following Drilling system shall be considered as SCE:
All drillings systems equipment should be inspected in accordance with the following industry standards:
- API 4F Drilling and Well Servicing Structures:
- API RP 4 G Operation, Inspection, Maintenance, and Repair of Drilling and Well Servicing Structures:
- API – RP 8B / ISO 13534:2000 Inspection, Maintenance, Repair, and Remanufacture of Hoisting Equipment
Performance Standard Assurance Tasks
Assurance tasks will used as specified in:
- PR-1312 – Well Engineering Equipment Inspection Procedure and PDO Drilling Equipment Inspection Manual part I and II
- Drilling system assurance tasks will used as specified in the Global Performance Standards Rev 6.
- SAP CMMS SCE Implementation: The SCE Classification will be assigned at the equipment functional location.
- The Performance Standard Required Y/N flag will be set to YES.
Exclusion from SCE Identification Scope
High pressure equipments related to well control is excluded in this group
Typical Equipment
- Drilling and Well
- Servicing Structures and hoisting equipment
- Drilling / well service Mast, Substructure
- Racking / Stabbing Board, Crown Block
- Travelling Block
- Drilling Hook
- Links Elevator
- Elevators (all type)
- Rotary Table
- Kelly D. Bushing
- Master Bushing
- Slips
- Spiders
- Safety Clamp
- Tongs
- Kelly Spinner
- Brake Bands & Linkages
- Dead Line Anchor
- Lifting Plugs
- Air Winches
- Power / Rotary Swivels
- Spelters
- Trailer King Pings
- Slings & Shackles
- Personnel Basket
- Cranes (Hook Inspection)
- Forklifts (Fork & Forks Support)
SCE group 2 – Well Control Equipment
Boundary Conditions Drilling Well Control Equipment
All well control equipments will be considered as SCE
Assurance tasks will used as specified in
- PR-1312 – Well Engineering Equipment Inspection Procedure and PDO
- Drilling Equipment Inspection Manual part I and II
- As detailed in WS 38.80.31.32-Gen. Pressure control manual
- Drilling system assurance tasks will used as specified in the Global Performance Standards Rev 6.
SAP CMMS SCE Implementation:
- The SCE Classification will be assigned at the equipment functional location.
- The Performance Standard Required Y/N flag will be set to YES.
Exclusion from SCE Identification Scope
There are no exclusions from SD008 scope, all well control equipments will be considered as SCE.
Typical Equipment
- Ram type BOP
- Rod BOP
- Annular BOP
- BOP control unit
- Drilling Spools & Flanges
- Hub Clamps
- Choke & Kill lines
- Cement Line
- BOP Shooting Nipple
- Chicksans
- Manifold & Valves (H/P)
- Standpipe & Hoses
- Pulsation Dampers
- Gas Cylinders
- Air Pressure Vessels
- Relief Valves (Mud Pumps)
Execute performance assurance tasks
For SCE group 1 and 2 the SCE’s performance assurance tasks are carried out to check whether the SCEs are working as required and to identify corrective actions, where required. The essential supporting maintenance process must be detailed in Drilling equipment inspection manual.
The outcomes are completed performance assurance tasks, recorded results; follow-on work initiated for failed performance checks and performance assurance tasks that have not been completed on time.
Analyze results
The results of the performance assurance task shall be assessed in order to determine if the performance meets the acceptance criteria. If the outcome is “passed” or “failed and fixed”, no further action is required. If the outcome is “failed”, it is classed as a non-conformance
Manage deviations
The risks associated with deviation in performance assurance tasks are assessed and appropriate mitigating actions to be taken to maintain control of the risks. Mitigation plan must be in line with Maintenance and Inspection Activity Variance Control Procedure